Производитель арболитовых блоков размерами 500×400×200, 500×300×200, 500×150×200 мм. Оказывают услуги строительства.
Производство арболита в Златоусте открыто в июле 2017-го года. В цеху работает 3-4 человека. Продолжительность смены – 8 часов. Месячная производительность – 240 кубов. Уход за оборудованием (смазка и чистка) осуществляется ежедневно.
Решили производить именно арболит, потому что это более теплый материал. А также крепкий. В Челябинской области в основном делают шлакоблок, а это же просто камень – никакого тепла. В арболите же 90% дерева, а дерево – самый теплый материал. Антон, начальник производства.
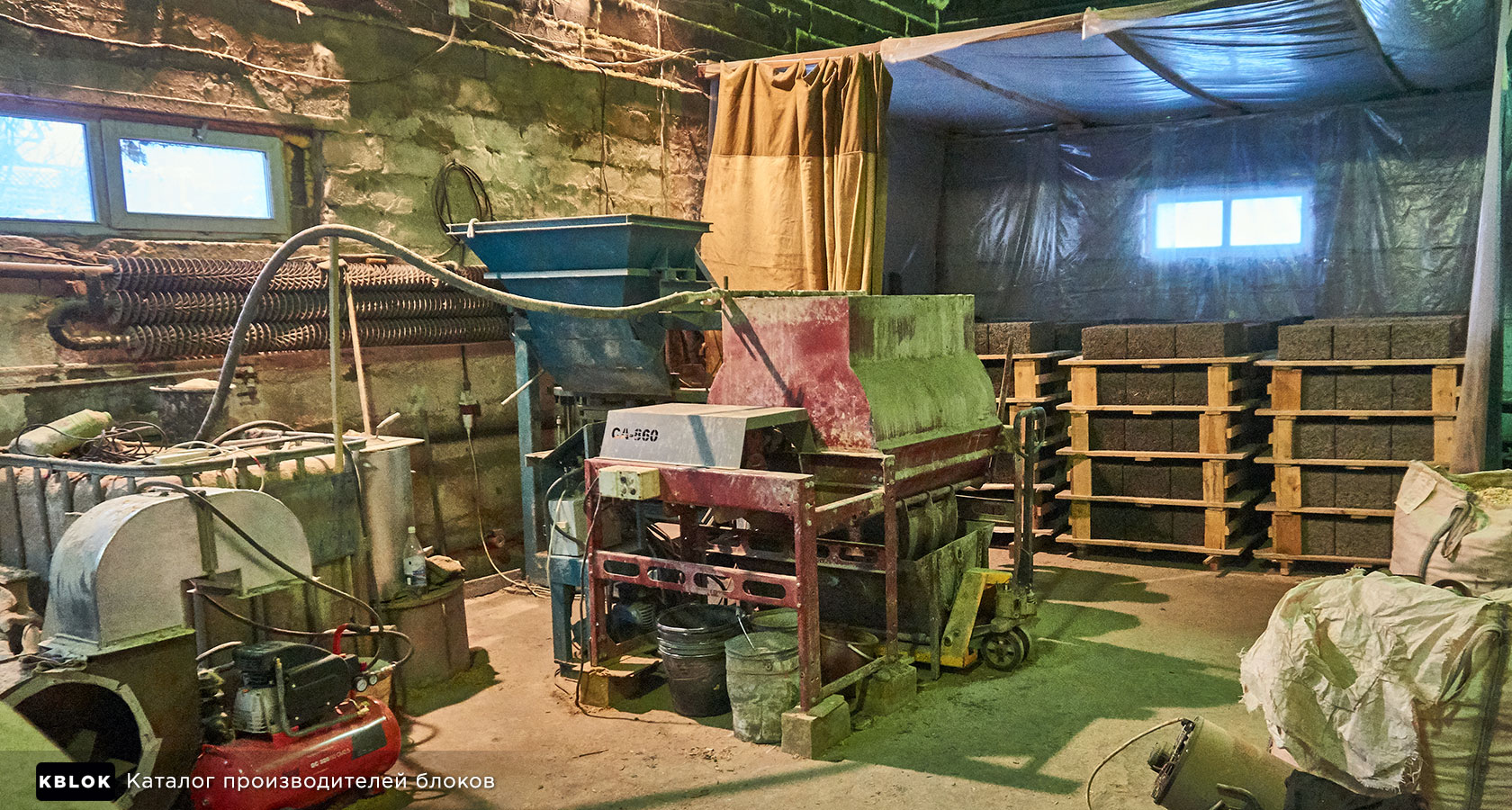
Сырьем для древесной щепы служит сосна. В городе много пилорам, работающих с этим деревом, поэтому недостатка в сырье нет.
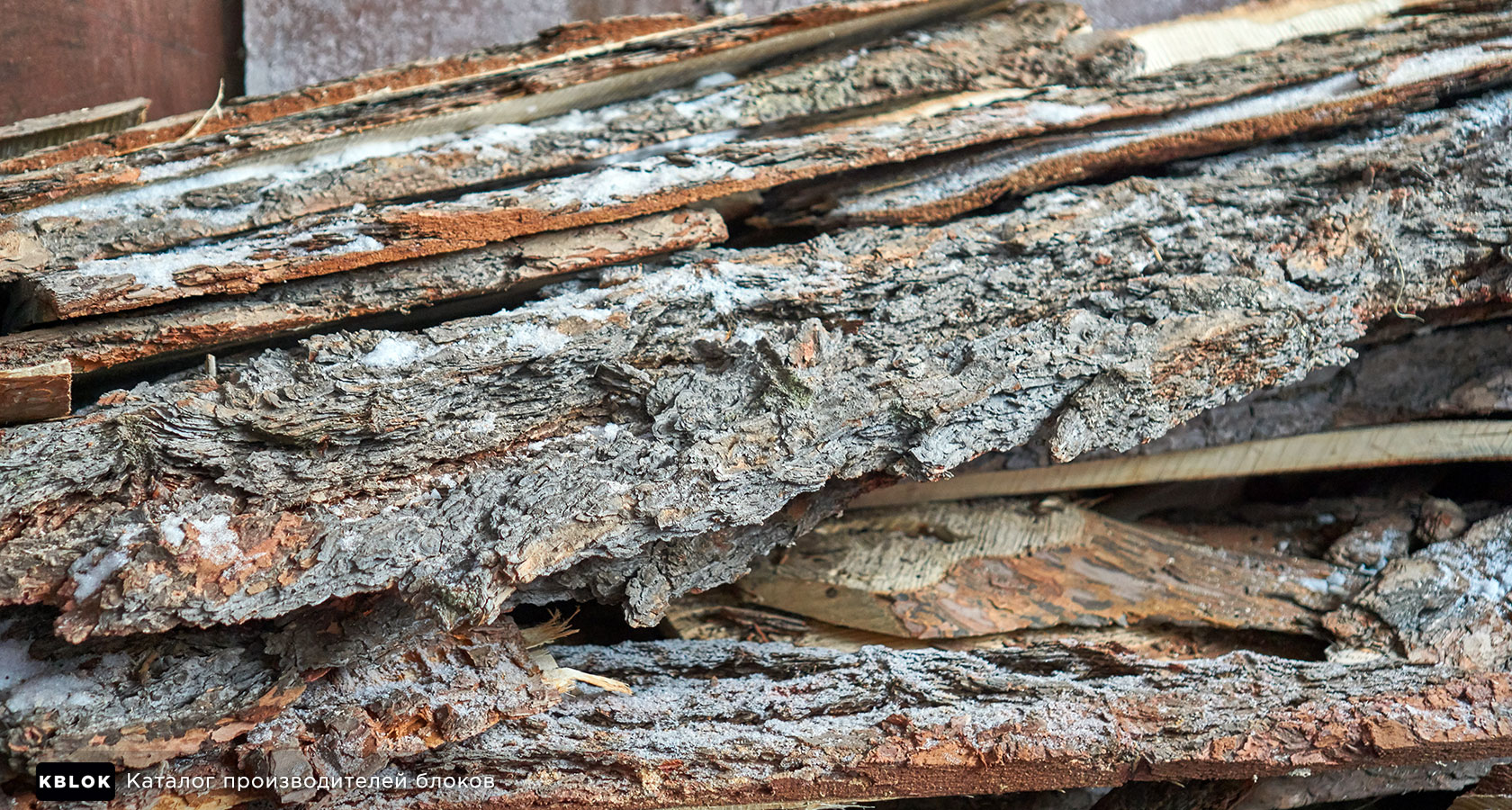
Перед обработкой на щепорезе горбыль очищается от коры.
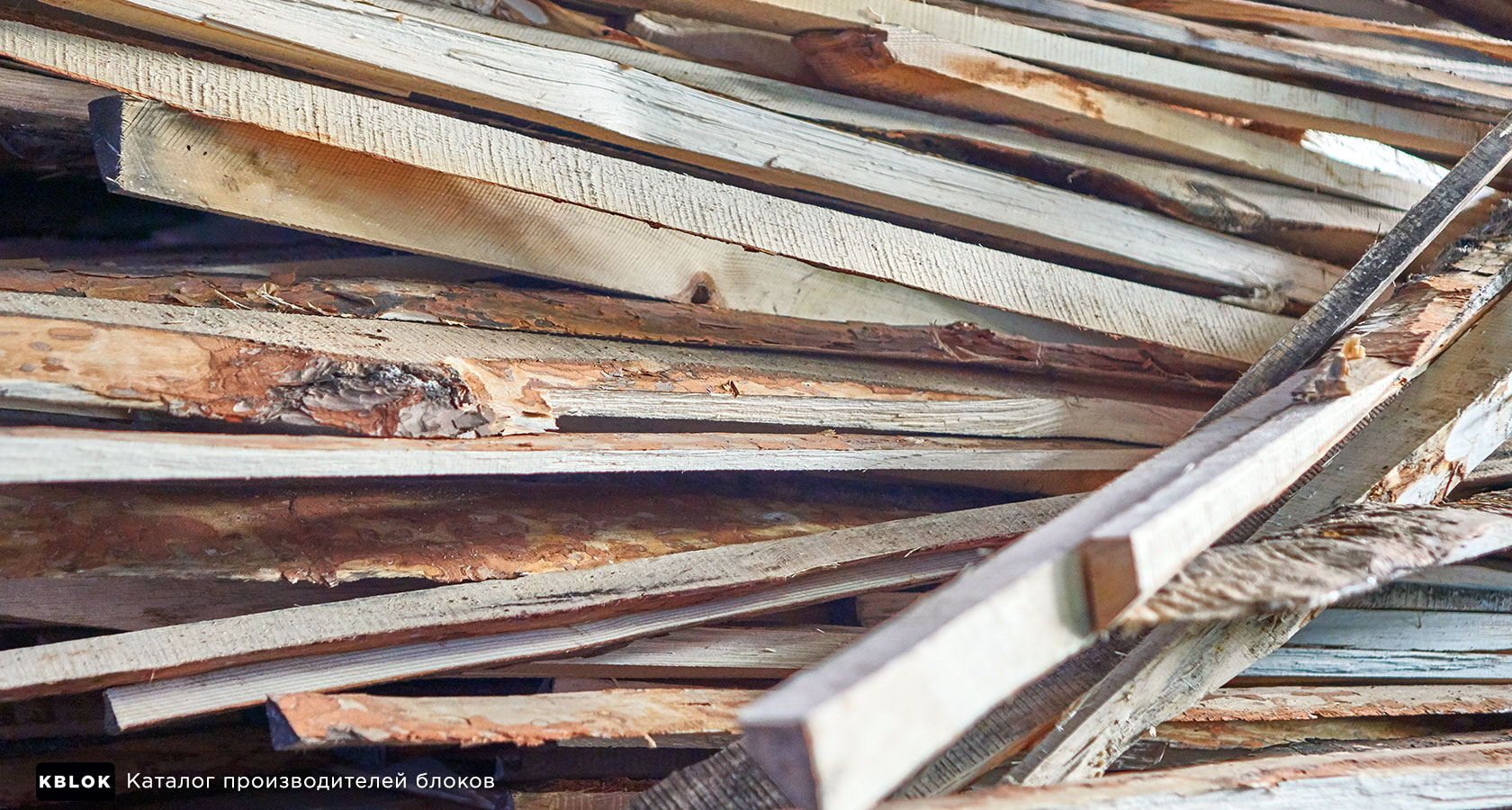
Используется щепорез «Станки-Урал» челябинского производства. Поначалу был куплен другой, но он не понравился, пришлось его возвращать и искать новый.
На первом получалась квадратная щепа типа технологической. Блоки на ней мне не особо понравились, углы осыпаются, – рассказывает Антон, – а на челябинском гостовская, игольчатая щепа. Клиентам, которые посещали производство, она понравилась. Как и нам. Антон, начальник производства.
Ножи в измельчителе затачиваются каждые две-три недели.
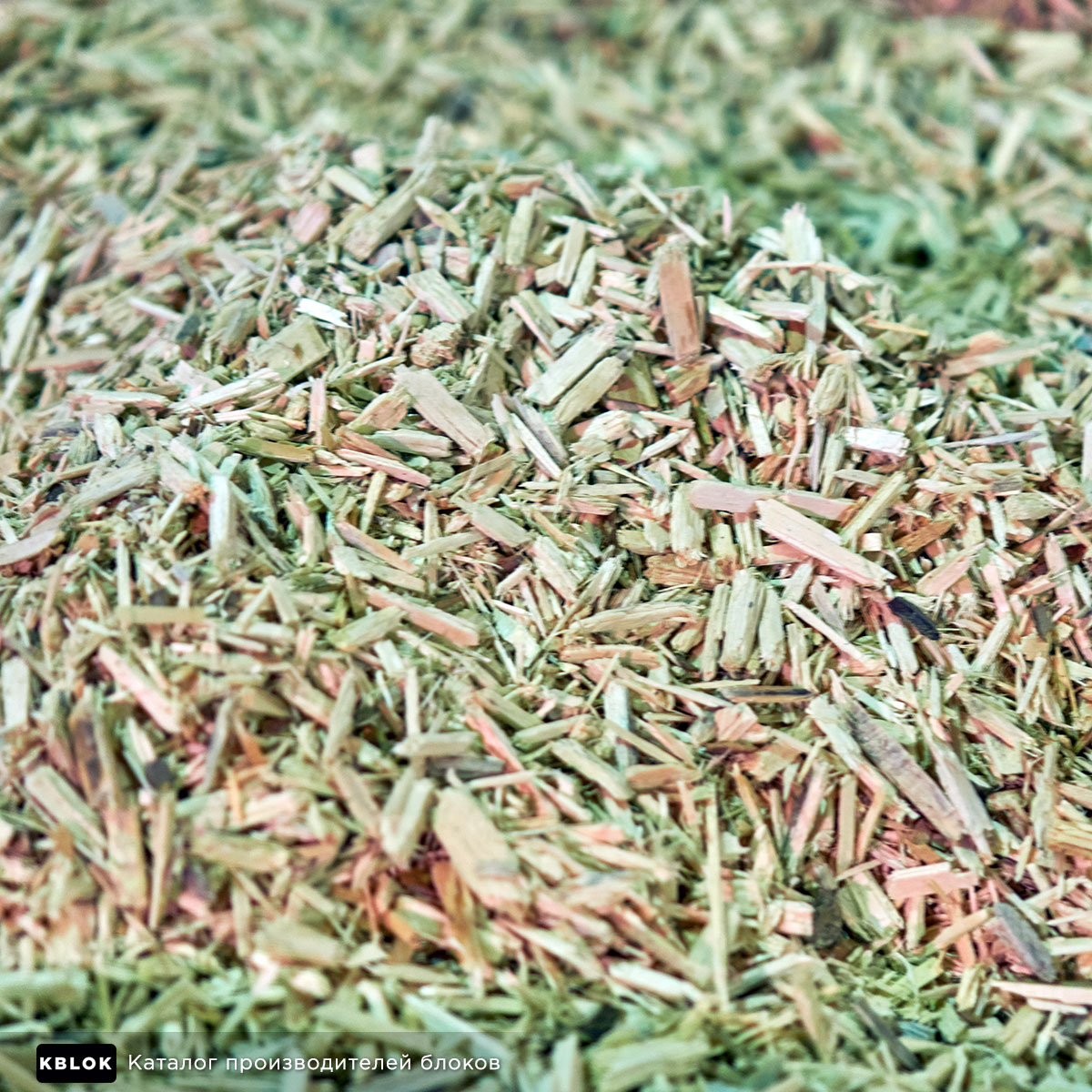
Для нейтрализации древесных сахаров используется кусковой сульфат алюминия. Перед замесом он в течение суток растворяется в кубитейнере с водой.
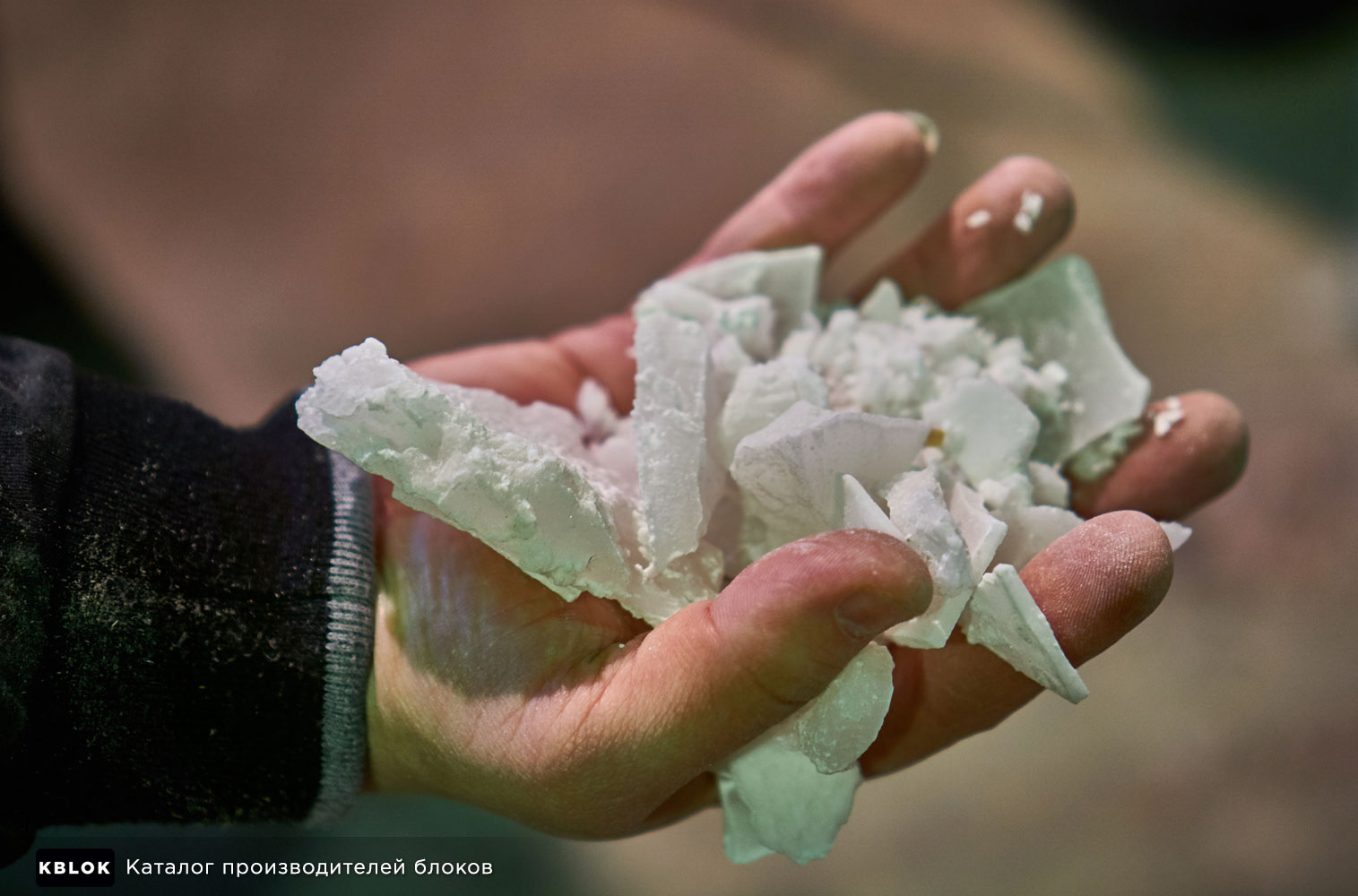
Для замеса арболитовой смеси используется барнаульская бетономешалка с горизонтальным валом. Процесс смешивания компонентов стандартный – сначала засыпается щепа, затем подается вода с растворенным в ней сульфатом. Насос качает определенное количество воды из кубитейнера и подает в смеситель. Чуть позже добавляется цемент 500-й марки без добавок. Цемент приобретается в компании «Катавский цемент» («Евроцемент груп»).
Готовая смесь высыпается в специальную емкость под смесителем, затем с помощью тельфера подается в бункер вибропресса. С одного замеса получается 9 блоков.
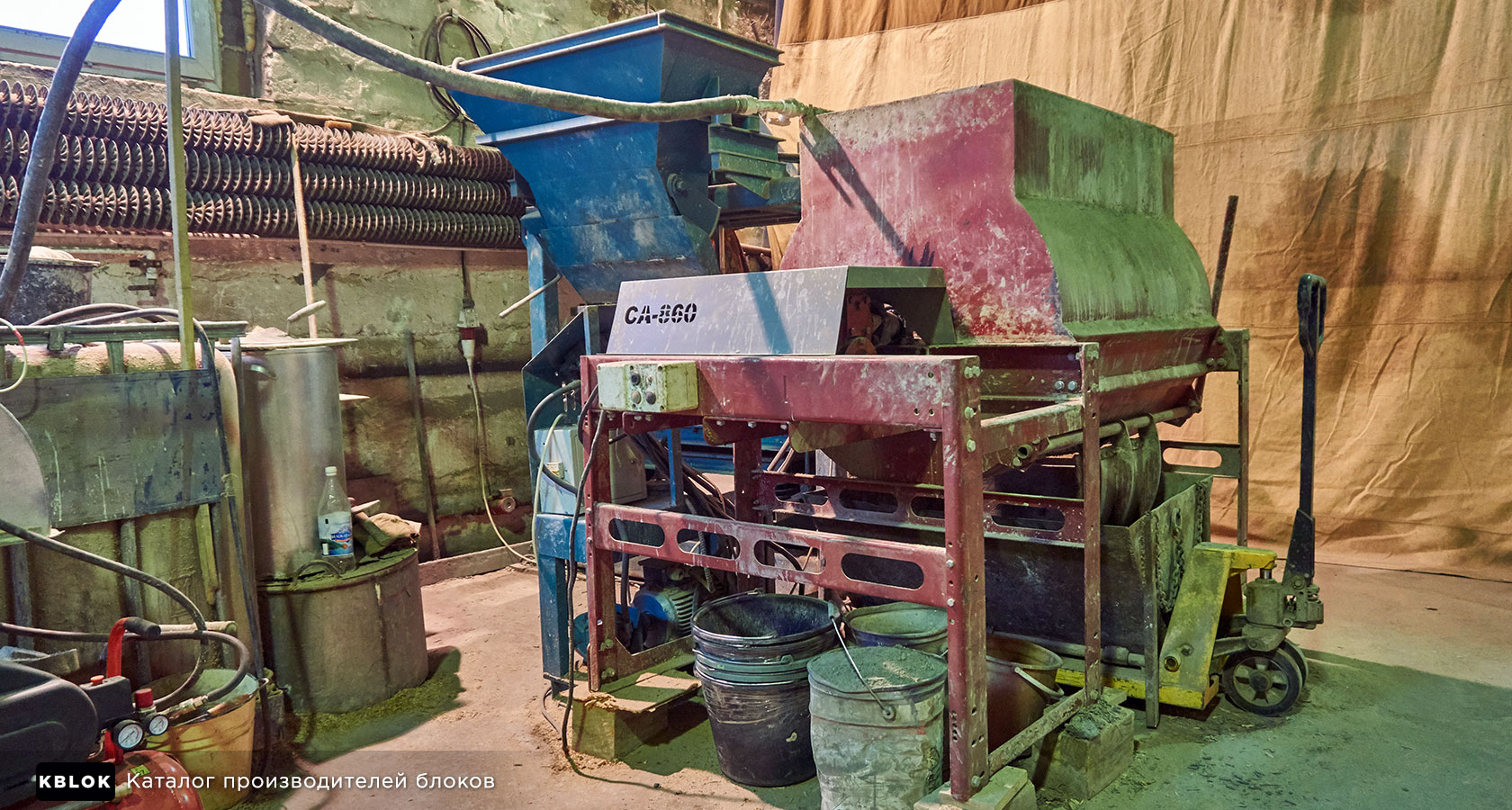
Вибропресс приобретен в одной из кировских компаний и совместно с производителем улучшен и доработан. Одно из улучшений – увеличение числа вибраторов, другие – держатся в секрете.
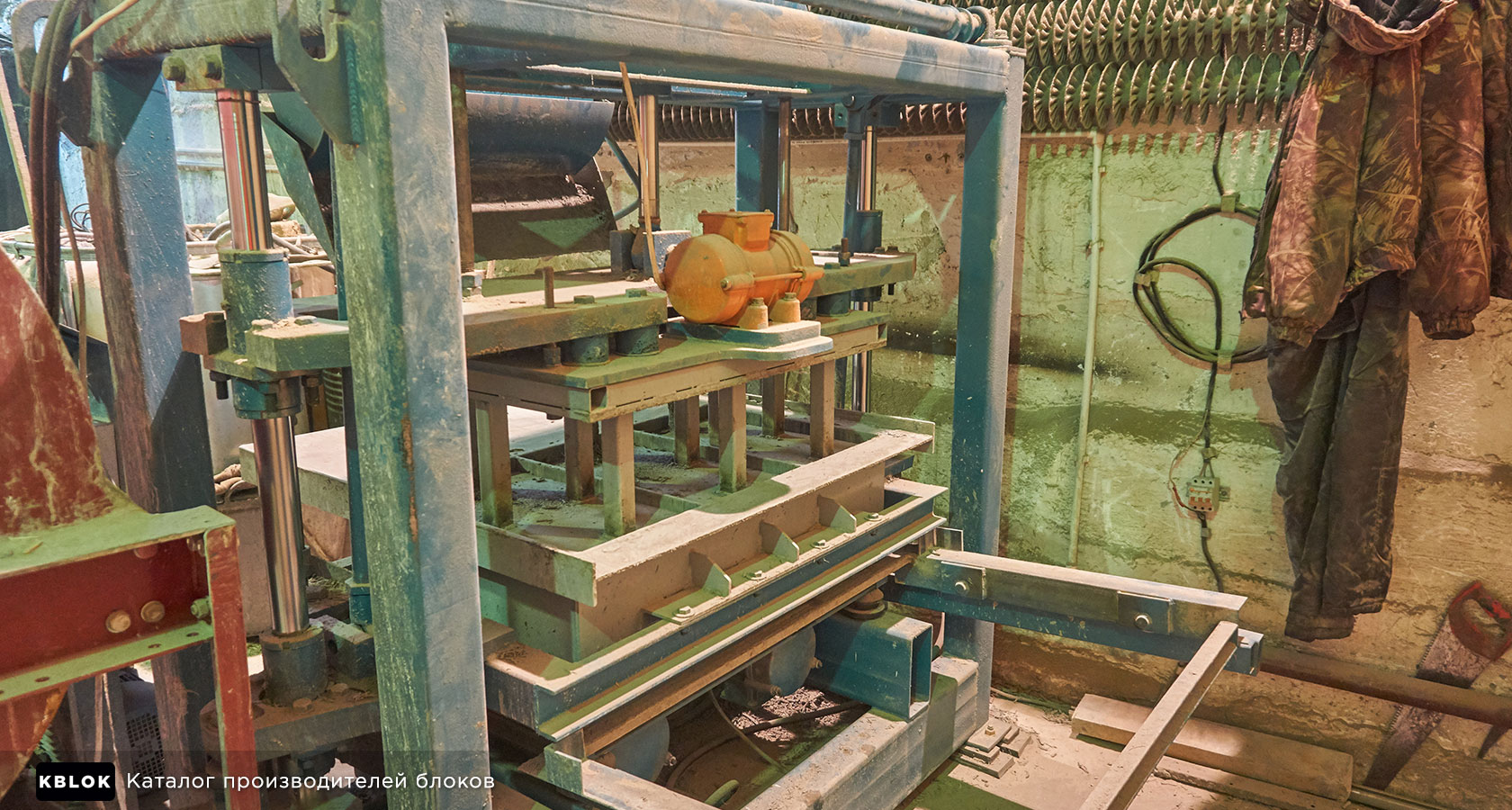
Изначально пресс был куплен с матрицами под блоки 500×400×200 мм. Также на местном заводе FORMANTA заказаны матрицы под размер 500×300×200 мм.
Нижней площадкой при вибропрессовании служит деревянный поддон, обработанный на рейсмусе. После формовки поддон с готовыми блоками переносится в сушильную камеру, отапливаемую теном.

Температура в сушильной камере 20 °С. Блоки здесь хранятся в течение 3-х дней, а затем складываются на поддоны. Когда требуется увеличить производительность, температура в сушилке увеличивается и уже через сутки блоки переносятся в другое помещение, температура в котором не ниже 15 °С. Там блоки отстаиваются перед отгрузкой еще две недели.
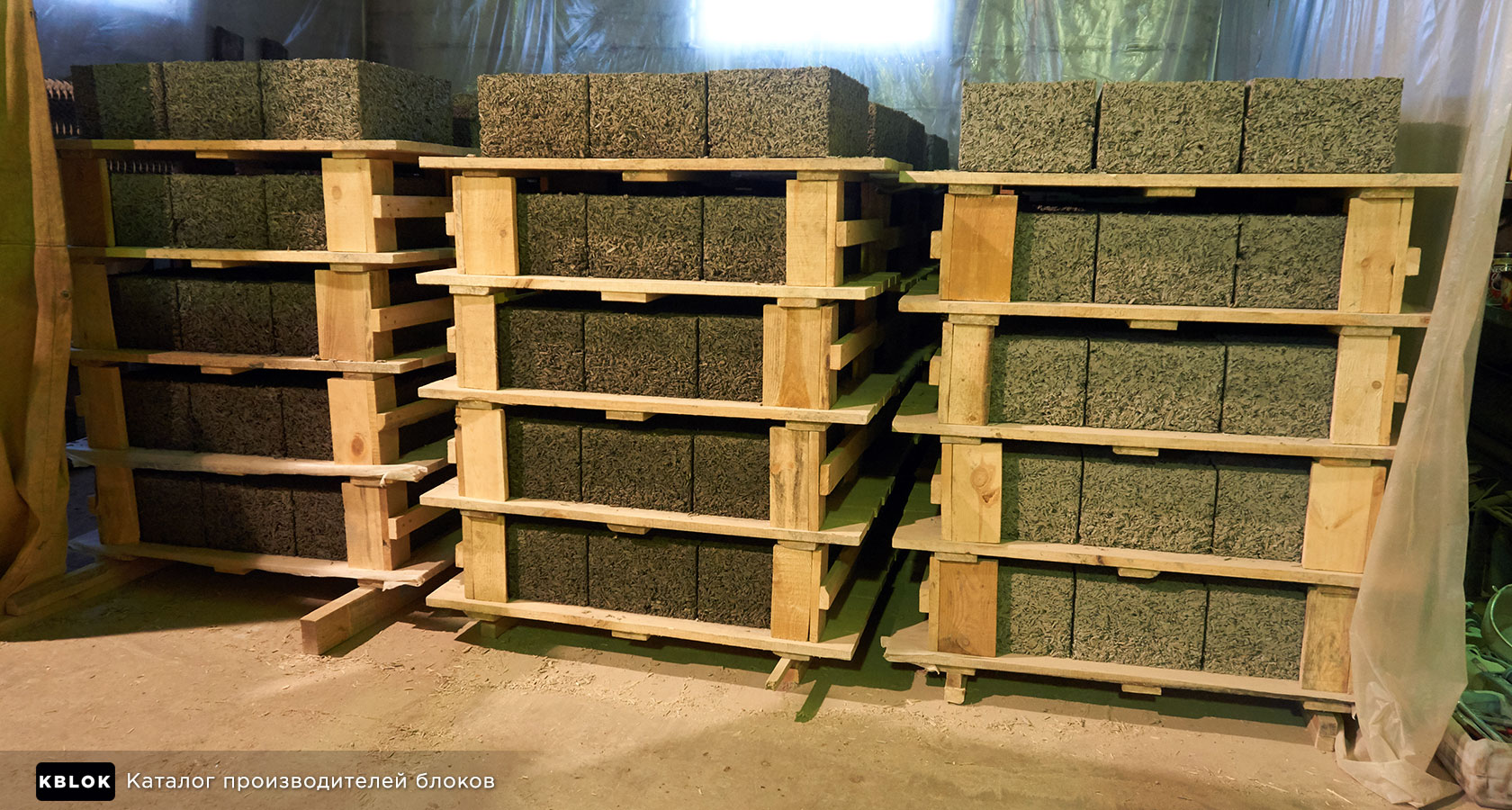
Еще на этапе запуска производства, как только были сделаны первые блоки, компания АРБОБЛОК74 провела испытания. Получен сертификат соответствия, а также протоколы испытаний.
Характеристики производимых блоков:
- плотность – 610 кг/м3;
- прочность – М25;
- теплопроводность – 0,11-0,12 Вт/(м·K).
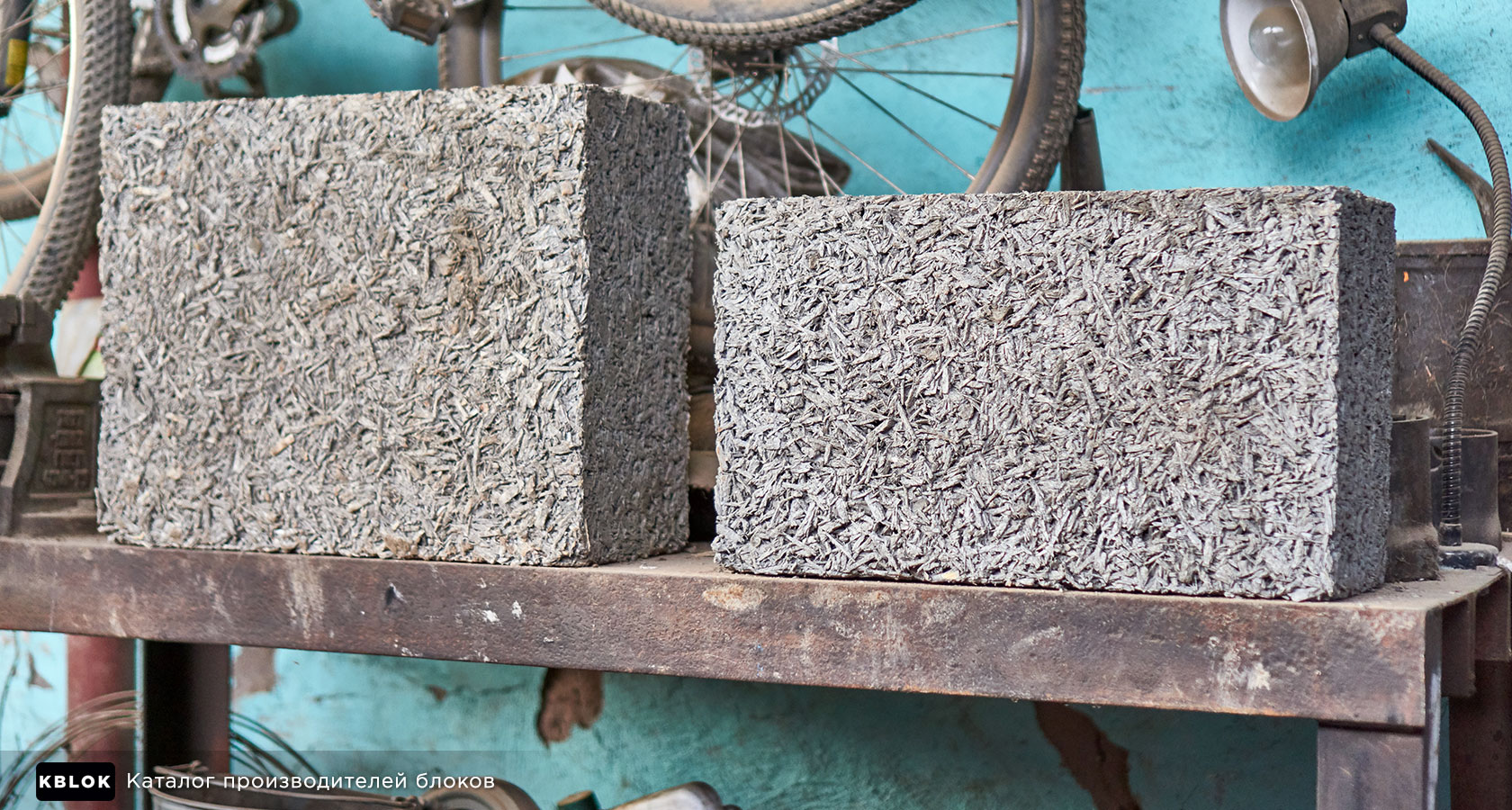
У нас хорошая геометрия, и плотность, и теплопроводность. Испытания сделали сразу, чтобы быть честными и перед собой, и перед клиентами. Антон, начальник производства.
В 2018-м году планируется модернизация (обустройство транспортерной ленты и шнеков) в сторону большей автоматизации производства для увеличения производительности.
В собственности компании имеется автотранспорт для доставки блоков.